How do we determine the Condition Rating of your Safety Valves?
Read a more detailed information about how we determine Safety Valve Health
“As New” Condition
Within the manufactures design and build tolerances,
little or no deterioration
A safety valve in new condition, within the manufacturer’s design and build tolerances, means the valve is in pristine working order and ready to fulfil its critical safety function. Here’s a breakdown of what that entails:
Flawless Construction:
Imagine the valve as if it just rolled off the assembly line. All its internal components are perfectly machined and free from any defects or imperfections. Springs are under the designed tension, seals are spotless and flexible, and the opening mechanism operates smoothly.
Precise Calibration:
The safety valve is set to release pressure at a specific point, following the manufacturer’s specifications. This ensures it won’t activate prematurely or fail to open when needed. This calibration is often documented with a certificate or tag attached to the valve.
Unimpeded Operation:
There’s no internal or external restriction that could hinder the valve’s ability to open and vent pressure. This includes a clean flow path for the fluid and proper installation without any external stress on the valve body.
Reliable Performance:
Within these ideal tolerances, the safety valve is guaranteed to perform exactly as intended. When pressure in the system reaches the designated limit, the valve will open reliably, releasing excess pressure and preventing catastrophic system failure.
Signs of Deterioration
A valve that will still protect the system but is showing
signs of deterioration
A valve is a device that controls the flow of something, like a liquid, gas, or even sound. While it might still be functioning, a deteriorating valve can show some warning signs that it needs attention soon. Below, we’ll go through what a valve showing signs of deterioration might look like:
Reduced Efficiency:
Imagine a valve designed for high flow. If it’s deteriorating, it might struggle to maintain that flow rate. This could show up in a system as reduced pressure or lower volume on the output side.
Leaks:
A valve’s job is to seal and control flow. A deteriorating valve might develop leaks, allowing some material to pass through even when closed. This could be a small drip or a more significant flow depending on the severity.
Unusual Noises:
Valves open and close smoothly under normal conditions. Worn parts or a build-up of debris can cause the valve to make grinding, screeching, or chattering noises during operation.
Changes in Operating Characteristics:
A valve designed to operate easily with a certain amount of force might become harder to open or close as it deteriorates. This could require more effort to operate or show signs of struggling during automated processes.
It’s important to note:
Even if a valve is still working somewhat, these signs shouldn’t be ignored. A deteriorating valve can fail completely at some point, potentially causing damage or downtime to the system it protects. Early detection and replacement can prevent these bigger issues.
Absolute Limit
Absolute limit of acceptability, the valve is not guaranteed
to protect the system and needs testing immediately
Don’t Gamble with Safety:
Critical components can deteriorate over time, raising a red flag when their reliability becomes questionable. Here’s what you need to know about safety valves nearing their limits and those deemed unfit for purpose.
Safety Valve at the Absolute Limit of Acceptability:
A safety valve operating at the absolute limit of acceptability is a precarious situation. This means the valve has exhibited concerning signs during testing or inspection, raising doubts about its ability to perform its safety function flawlessly. Here’s what this might look like:
Sticking or erratic operation:
The valve might hesitate to open when pressure reaches the set point, or it might not fully close after venting, potentially leading to leaks or delayed pressure relief.
External leakage:
Visible signs of leakage around the valve body or bonnet indicate compromised seals, jeopardising the valve’s ability to contain pressure effectively.
Internal corrosion or damage:
Internal inspections might reveal signs of corrosion, erosion, or physical damage on critical components like the spring or seat, compromising the valve’s ability to withstand pressure.
Immediate Testing is Crucial:
When a safety valve shows signs of being at its absolute limit, immediate action is essential. This involves doing the following actions:
Isolating the equipment:
The equipment protected by the suspect valve should be taken out of service to prevent potential hazards.
Absolute Limit
Detailed inspection:
A qualified technician should perform a thorough inspection of the valve to identify the root cause of the issue.
Pressure testing:
The valve’s functionality needs to be rigorously tested using specialised equipment to confirm if it can still meet the required pressure relief settings.
Safety Valve Unfit for Purpose:
In some cases, a safety valve might be deemed entirely unfit for purpose. This scenario occurs when the valve is so damaged or malfunctioning that it poses a safety risk itself. Here are some signs:
Complete failure to open:
The valve shows no signs of opening even when pressure exceeds the set point, rendering it useless in an over-pressure event.
Severe corrosion or cracking:
Extensive internal or external corrosion, or cracks in the valve body, significantly compromise the valve’s structural integrity.
Missing or damaged critical components: If essential parts like the spring or seat are missing or inoperable, the valve loses its pressure relief functionality.
Immediate Replacement is Mandatory:
If a safety valve is deemed unfit for purpose, immediate replacement is mandatory. There is no room for compromise when it comes to the safety of your equipment and personnel. A qualified technician should install the new valve according to manufacturer’s specifications and perform the necessary testing to ensure proper operation.
Contact Us
Our service engineers here at Seetru Engineering Services have extensive knowledge and experience of safety valve testing, maintenance, and lifecycle management. We also provide complete overhaul services for your safety valves. We recommend that you contact our team to discuss your requirements.
Contact SES
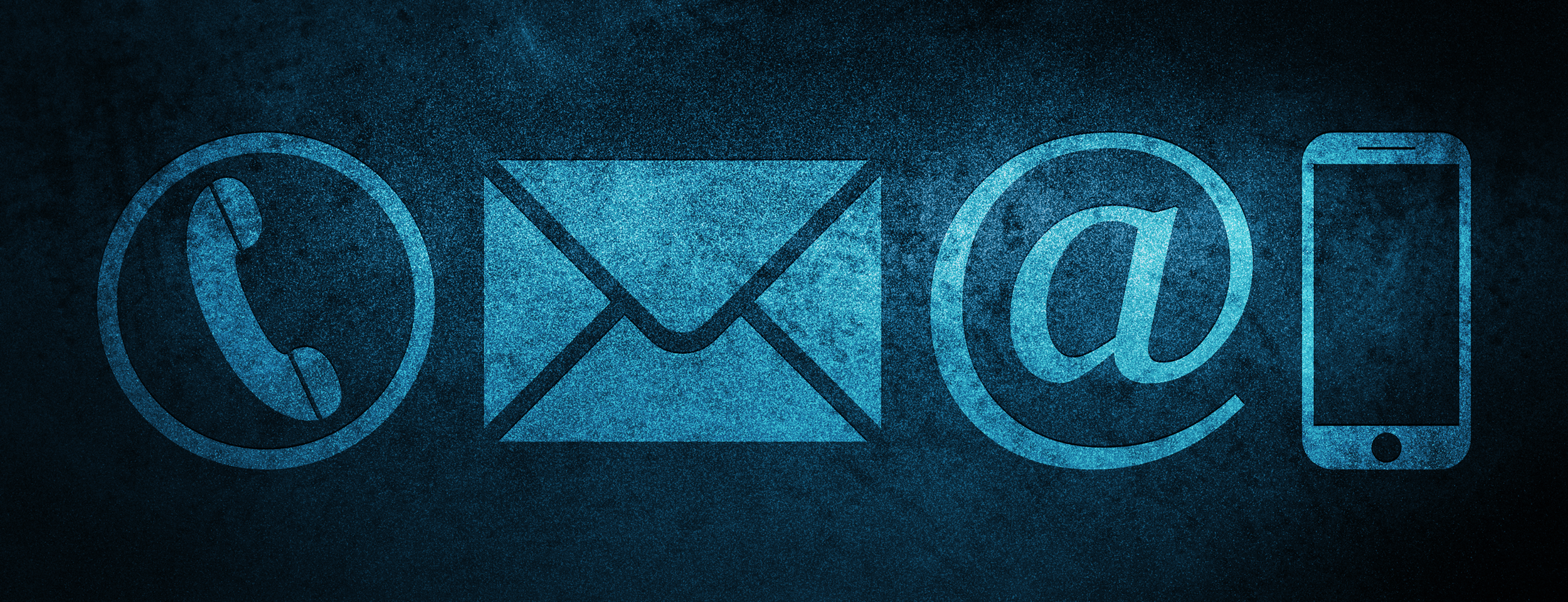